I am a former Marine and a current Police Sergeant in Alabama. Feeling a little under-qualified. Haha. Glad to be able to soak up all of the combined knowledge.
Don’t worry, you’ll fit right in — 5 years in the Air Force here, including working as a Security Police.
I was a little nervous about venturing off into the land of CNC. I mainly got involved for woodworking purposes. I’m sure you guys in the forums hear this all the time, but the community is what sold me on Carbide products. When I was lurking around the different posts trying to gather information I noticed there is a core group of people on here that seem to find joy in helping others solve their problems. After seeing that I figured I couldn’t go wrong here. So, thank you guys for unknowingly motivating me to get out of my comfort zone and learn something new.
Caleb
Retired grandfather and life-long tinkerer, born and raised in So CA. Married, 1 son, one grandson.
USCG Avionics Tech / SAR crew member on HU-16 Albatross seaplanes back in the 70’s.
AA degree in Electronics, followed by 40+ years in Medical electronics, 34 of them as a Field Service Engineer on automated microbiology, virology and DNA hardware. Retired at 62 after a life mostly on the road, throughout western USA and Canada.
1/3 of our 3-car garage is my shop. Mostly woodworking, with some electronics and welding. Got my S3XL over a year go, assembled it, and left it in a corner. After some prodding by my programmer son, I pulled off the tarp and dove into CC & CM. Cut myself a set of clamps and was hooked. Built a massive cart, planning an enclosure. The tinkerer in me sees at least a dozen ways I want to Hot-Rod the S3XL to make it even more capable. Working on a novel work-holding / dust collection system. If it pans out I’ll share some photos later.
Graphic Designer/Typographer designing and programing business forms for a financial company. Prior ran a printing company and managed a medical equipment company. Also 10 yrs as a copier tech and pressman.
Woodworking hobbist, woodturner and home renovator.
Did some work in the field of medical visualization and am now a software developer. Doing some woodworking is a great compensation for all that work in front of the monitor (though, designing the parts adds to my screen-time ).
I am retired senior software developer, and a full time CNC student.
Yep, I am way underqualified. lol
I am retired (medically) military. worked as a combatives instructor for a awhile. Some how I ended up getting paid to sharpen knives and straight razors, as well has replacing handles and handle scales on them. I’ve always enjoyed wood work, carving, building. Decided to buy a cnc machine, and Shapeoko seemed the way to go. Having never messed with any thing like this my wife thought I was nuts. For the record she still does. lol.
I am a cnc programmer at Production Machine & Tool in Wichita Falls, Tx. I have worked there since 2006 ( I was 19) and ran/setup the machines for 7 years. Worked on the weekend to avoid putting our kids in daycare which gave me lots of time during the week. I was big in PC building at that time and at that time mine was water cooled, running dual graphics cards. I wanted to water cool them but couldnt find on for them or they were insane expensive so i wanted to make my own… so I got a hold of a copy of Mastercam, having zero idea how to use it, and somehow designed a water block and ran it at work while on the clock lol. I showed my boss and the owner and they moved me into programming within a few weeks! Crazy how things work out like that… Now we have a bunch of horizontal mills, lathes, 5 axis lathe/mill, and recently we got HUGE boring mills which some have contouring heads(look them up, super cool) on them and 8ft quils(the spindle can be programmed to extend 8ft!). Anyway… now I use solidworks for cad and Esprit to program our machines at work and I am in my shop every day at home
A ‘reformed’ electronics/RF engineer, now run a manufacturing site for a high speed/high quality video transmission equipment Company. Tinker with electronics, modest software, love making things whether wood, metal or brick. A bit of a petrol-head, cars and bikes, and love adventurous travel, especially on the bikes. My workshop feeds these wants, gives me a change of focus from the hi-tech day job, and keeps me sane (my opinion). Recent projects: A complete, every piece made wood and brass long-case clock, various carved pieces of furniture, trinket boxes, trivets and the like. The clock has a Raspberry Pi ‘hidden on the back’ complete with my design of interface ‘HAT’ for monitoring accuracy, drift and for attempting to correct timing. My CNC is ShapeOKO 3 XL with Dewalt spindle, modified Z-axis to use open-ended belts, steel core GT2 belts all around (really interesting thread on this topic running at the moment). Use a mix of Solidworks, Vectrics VCarve, CC and CM (all on Apple) for designing and making. Currently working on a Sistine-esque fresco carved pair of cupboard doors
I had the pleasure of being a heavy equipment operator that got to run one of the most challenging but versatile excavator machines on the planet for a few years. A Menzi Muck A91 with a flail mowing head, 360 degree grapple, and a 3 ft bucket. I was tasked with climbing the machine into our City’s Drainage canals and ponds to mow, dredge, and maintain them. After we got hit by 3 major hurricanes in a row I used the grapple to clear fallen trees from the streets so EMS could respond to calls. The cab controls are like a fighter jet with 2 main joysticks that each has 3 mini joysticks and a few buttons to control the boom and legs and attachment tilt. On the floor are 3 bidirectional petals that control the wheel drive motion, the boom extension, and the hydraulic flow for boom attachments. Each leg can move in, out, up, and down. Fully retracted it can fit in a standard car parking space but extended can sit 15 feet wide and over 15 ft tall.
Forced to retire early due to a dirt bike accident that left me a C5 Quadriplegic at the age of 25, over 12 plus years ago. But I had a few great years in my Menzi that took my operating skills to a whole new level.
I miss running it beyond measure, although it was funny watching a guy twice my age with 15 years of track hoe experience think he could jump in my machine and run it solo with no climbing tactics training. Watching his eyes widen and butt pucker up when he didn’t watch his leg placement and machine center of gravity changed a 220 lb bearded biker into a scared school girl for a split second and it was priceless.
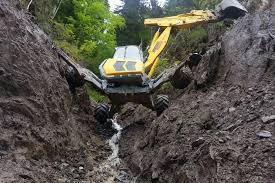
Now I run the information desk part time and use 3d modeling coupled with my SO3 and 3d printer to develop adaptive tools that make my life more accessible.
@AndyC - please tell me how to ‘reform’ out of RF Engineering - I really need to know
Started my own business, TV/CATV signal distribution world, tried to do all the things I felt were wrong in previous businesses… proved right on some things, not on others. Chance to join a customer’s business came up some years later doing Production Engineering/NPI/off-shore liaison and felt it was the right step. My previous partners carried on for another 8 years or so then lost interest and sold out to a rival. I do chuckle to myself every once in a while when I look at RF techniques I was familiar with turning up in today’s high-speed Digital electronics!!
12 years British Army as a Vehicle Mechanic, over 30 years Fire Service (24 operational and 6 ‘corporate’), now I own my own business as a fire safety consultant and just started my hobby with an XXL.
First project? Building an enclosure from old left-over materials from my pre-CNC projects!