Draw up the tool which will be used in profile:
and maybe that 1" Stock Thickness isn’t such a bad idea…
The geometry needs to be inset twice, once to define the thickness of the sides, and once to define the slope at the front/back — drawing these up in profile we get something like:
where we arrive at a problem which has presented itself in the past — drawing up a tangent to an arc… however, it should just work to maintain the same proportions at each edge so as to get a consistent rounding — we’ll see.
We subtract twice the width of each profile:
Done
This should get us geometry which when selected and modeled to the desired height:
will result in the desired slope/angle:
We then right-click on the geometry in question and choose “Create Outline Vectors”
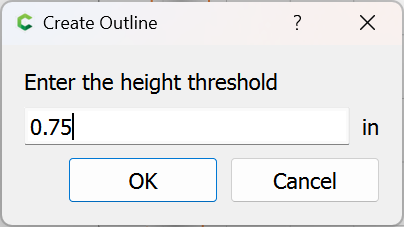
entering the desired height
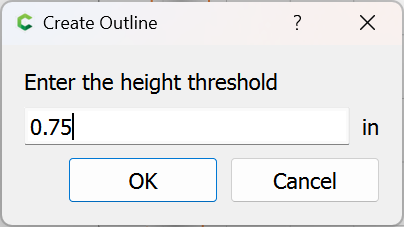
which does not have the desired result:
Backing up, we try re-examining the modeling to determine the difficulty:
and it becomes obvious that we will need to model past the Stock Thickness:
(indicated by the red area)
and adjust based on that.
We then Ungroup Vectors
and use the geometry for the top outer edge to model this flat and equal:
at the desired height yielding:
which shows that we are not getting the desired change in slope (due to allowing the additional projection) — re-working the geometry and model would seem to be called for…