A post about belt tension, how to measure it, what effect it has and why you need to manage belt tension in order to usefully calibrate and square the machine.
As usual, no criticism of the machine here, in fact some quite clever design choices seem to have been made.
The question of drive belt tension has been bugging me. How much you should have, how to check it and how it affects machine performance. I failed to find any quantitative data to use, so I went and started measuring; and found that belt tension is quite important if you want to square and calibrate the machine effectively.
TLDR
- Belt tension means belt extension, if your Y belts arenāt equal tension your machine canāt be square and your Y steps per mm calibration can only be valid for one X position. You can fix this pretty easily by using the frequency tuning method, twanging the belts and tuning both Y axes to the same note.
- The belt tensions easily achieved with the unmodified Shapeoko tensioner clips are well above the recommended shaft radial loads for a normal NEMA23 stepper. The results of persistent high radial load are fatigue failure (shaft snapping) and early bearing failure
- Measuring belt tension is easy and you can do it with a cheap luggage scale or a free phone app
- Checking belt tension as part of maintenance will likely warn you when the reinforcing members in belt a starting to fail
I so far have no reason to believe that increasing belt tension reduces backlash or otherwise helps the machine, at least within the linear range of tension on the belt and the radial load acceptable to the stepper motors.
I will be adding a belt twang to my regular machine checks, particularly to check the Y axes are balanced, Iāll also periodically take numbers with the phone app to check if my belts are going stretchy.
I will also not attempt to square or calibrate my machine in only one position, Iāll be checking back and front after balancing the Y belt tensions in future.
Hereās a video showing how to do the measurements.
Also, many thanks to @Julien for his assistance, suggestions and measurements from his machine.
Measuring ā Belt Deflection
The first method is to deflect the belt in the middle of a span and measure the deflection and force required, this is how belt tension gauges work on engines for Vee belts etc.
With the machine powered off push the X rail and Z carriage to their end-stops. Now mark the mid-point of the belt span between the drive pulley and tensioner , thatās about 450mm on the XXL.
On that mark place a block of about 25mm (1 inch) height for a long rail on an XXL or XL, or a block of about 10mm height for the short rail variant. With the belt in the normal position, mark the top of the belt on it and then measure the distance between the mark and the top of the block, thatās how far we will lift the belt from the normal position, our deflection d.
With the luggage scale looped around the belt, pull the belt up until the top of the belt is flush with the top of the block, a finger is sufficient to test this, and record the measured āweightā as our measure for the Deflection Force F.
Knowing the tension modulus of the belt from the vendor data (Gates) or measurements of the specific belt (thanks to the_real_janderson see thread) we can then stick these numbers into a simple spreadsheet and get the belt static tension on our machine.
Measuring ā Belt Tone
The much easier way to measure tension on the belt is to twang it and measure the frequency of the twang. For this Iām using the Gates Carbon Drive belt tension app for bikes. Itās free and measures in about the right range.
To measure the tension using the belt tone method we need to have a known length of belt that we can produce a clean tone from when twanged. To do this;
Measure and mark a suitable length on your Aluminium extrusion rail, Iām starting 200mm from the end-plate and using 500mm length, 280mm seems a good number for the shorter rails of a regular or XL machine.
Stick a small block or a ¼ inch cutter shank (thanks Julien) under the belt at each side of your marks, ensure you get the correct sides and that the distance of un-supported belt between the blocks is what you measured.
Now twang the belt, you should get a pretty clear tone without the slap of belt on rail or too much buzzing.
The Gates app is meant to be used for lower frequencies on bicycle drive belts, it seems to get confused once itās been open for a while so I close it and re-open it for each measurement. Put the phone mic close to the belt and twang. Youāll get a series of samples where the app is ātriggeredā by the twang and a frequency reported figure out a reasonable average for the āgoodā samples. Repeat for each belt.
Shapeoko, XL and XXL
So far, everything here has been about my XXL machine, how do the numbers compare for a regular sized Shapeoko or the short Y axes on an XL?
I had expected the short rails to show about twice the tension of the long rails as the tensioners have the same length bolts, this does not seem to be the case. It appears that the belt slip on the tensioner as you tighten the bolt works to regulate the tension into the target range pretty well.
This appears to be key ā the belt tensioner is trying to stop you breaking the stepper motors.
The next questions are along the lines of āWhat frequency and distance should I get on my machine?ā
Julien has tested at 275mm on his machine, 280mm is very nearly 11 inches soā¦
Squaring & Calibrating
So, what about squaring and calibrating?
If you want square joints and parts, itās key to get the base of the machine and the Y rails level and square. Itās also important to ensure that the X rail is square between the two Y rails. On mine I had to shim the X rail to get it reasonably close to square.
Typical measurements are
- Corner to corner and the Y endplate to Rail support plate distances to ensure the base is square
- That the X axis is square to the Y rail plates and Y rails.
Getting this basic geometry right is key to getting square parts from any machine.
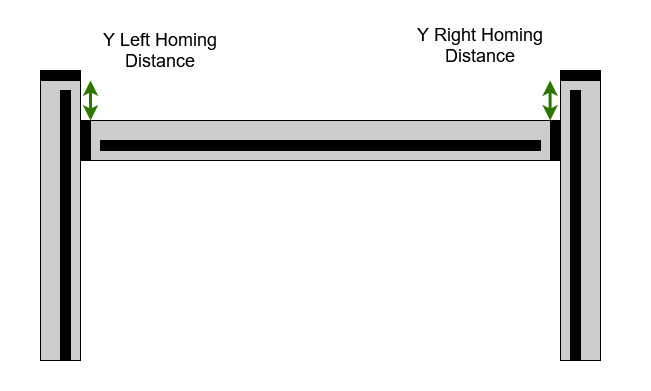
The problem is that we tension the Y drive belts by stretching them, this changes the tooth pitch of the belt which is what we base the GRBL $100 and $101 parameters on, 40 steps per mm. When the Shapeoko starts up it runs to the back of the Y rails to the homing switch on the right hand rail, assumes that the Y homing distance is good left and right and then takes steps forward from there on both Y motors, assuming that both Y have the same step distance.
If these two belts donāt have the same tension, assuming theyāre from the same batch and not worn out, they wonāt have the same pitch either, meaning that by the time your machine gets to the front, the X axis is misaligned. Also, your Y distances will depend on whether the Z carriage is further Left or Right. This is a bit of a problem if you want accurate or square parts, particularly if youāre using something like a vertical front mount for cutting dovetails.
(again, thanks to the measurements in this thread for the belt tension modulus data)
Taking all the values for my machine I checked this out to see how badly off I was.
My left and right Y axes were;
Those values seem reasonable given the available tensioning adjustment screw length.
If the numbers are correct then Iām 0.7mm off square just by jogging to the front of the machine, which makes a bit of a mockery of carefully shimming the X rail to be square with the Y plates (and also explains why when I use the edge finder on my framing square clamped to the spoil-board itās not squareā¦).
So, I measured the gaps between the Y carriage plate and the vertical steel Y rail supports at the back when homing and jogged all the way forward. Note that this measurement assumes that the Y end plates and Y rails have matching dimensions left to right;
Thatās a bit of a coincidence, 0.7 mm out of square by the time I get to the front, for a very small tension difference of only 3Hz, thatās from B2 to B2 flat.
I equalised the tones by releasing some tension from the left Y rail and re-measured, I now have 0.3mm offset at the front which is close enough without some much more detailed measurements.
Next up - How much is too much? and Math(s)